Using Floor Trusses in Modern Design
- Clements Wimsatt Architects
- Apr 21, 2023
- 5 min read
Most buildings built in the United States these days are built from wood. Wood is in fact a renewable resource, affordable, easy to work with, and provides enough strength for most projects. Wood products range from commodity lumber (2x4s, 2x6s, etc.), engineered lumber, (LVLs, Plywood, etc.), and pre-fab trusses. In today's blog, we discuss floor trusses and what benefits they offer to both single-family homes and multi-family projects.

The Challenges of Modern Design
Floor trusses have shown to be very effective in our projects at the company. The majority of our work, as you may know, has a more contemporary aesthetic. In contrast to more traditional architecture, designing a modern project—especially a modern home—reveals some significant difficulties. To attain simpler forms, the majority of modern structures, for instance, have flat roofs as a significant component. Your ability to conceal ductwork and HVAC equipment in what would otherwise be an attic area is limited by the flat roofs of these structures. The open floor layouts found in modern homes are yet another issue. Although not exclusively associated with modern architecture, open floor layouts pose structural problems because of the large spans required to execute them. These lengthy distances can be uncomfortable due to the bouncy surfaces that shake when people walk on them. Another area of concern regarding modern design is the housing shortage. Contractors these days have a difficult time keeping up with the demand especially when modern work comes across their desks. Modern projects are notorious for being more challenging to construct since simple forms frequently conceal complexity. Understanding trim is the key to comprehending this. Trim, such as exterior siding or crown molding, gives the craftsman installing the products a chance to cover up defects. Trim is typically purposefully omitted from contemporary constructions to provide more straightforward forms. As a result, the contractors must be more meticulous in their work further slowing down the process and further contributing to the housing shortage.
Solutions with Floor Trusses
Once again, without the benefit of an attic, it's difficult to place HVAC equipment without taking valuable closets or ceiling height to accommodate. This is where the floor trusses begin to help. Trusses can be designed around beams or HVAC because they come in a variety of shapes and sizes and offer a lot of flexibility without sacrificing structure. Most of the homes we design use oversized floor trusses to allow for the flexibility to hide ductwork, lighting, and other equipment. Using standard engineered or commodity lumber would require equipment penetrations through the structural members sacrificing their strength. With floor trusses, you can simply run equipment through the webbing or provide horizontal chases in the trusses to provide the space needed.

Because we all like our open floor plans most lumber especially commodity lumber simply cannot keep up. In addition, the increased demand for lumber with the housing crisis means that tree farms are being harvested with less mature trees than in the past. This pre-mature harvesting does not give the trees time to grow and strengthen resulting in weaker lumber. Floor trusses allow us to meet the span needs of the open plan without creating uncomfortable bouncy floors by designing with undersized products. Truss manufacturers engineer each truss to fit each condition of the project. Because each truss is designed for each condition, upon leaving the factory each truss is numbered and delivered to the job site in a specific order. Once on-site the contractor places each truss following a shop drawing allowing it all to go together like a giant erector set. This allows for a faster build time resulting in a quicker turnaround for the home builder. That is if there are not any "truss repairs."
Challenges with Floor Trusses
Trusses themselves come with their own set of challenges. These challenges are far less problematic but need to be understood nonetheless in order to take advantage of their potential.
Building Code Challenges:
The first set of challenges is related to the building code, more specifically fire protection. In a standard floor assembly using commodity or engineered lumber, the floor assembly is naturally divided into individual spaces located between each member. These divided spaces prevent fire from traveling quickly through the floor system. Such is not the case with floor trusses. As stated above floor trusses creates a benefit related to HVAC and ductwork but this also, however, creates a fire issue. Luckily there is an easy solution. If a fire were to occur and get into the floor truss assembly it could then quickly spread throughout the entire structure by traveling, like the ductwork between the webbing of the trusses. To prevent this from being an issue the international residential code states that "draft stopping" must be installed to prevent the spread of fire. The code states the following:

Draft stopping is usually just a layer of drywall placed in the cavity of the floor system. Check your local building code for more detail. Another code-related issue depends on the floor-to-floor height of the project. It's not uncommon to have 2' floor trusses and 10' ceiling heights. If you add in your standard stud wall heights (10'-1.25") your height of the floor truss, subfloor, and floor finish. You are easily higher than 12' floor to floor. Just know that there is an area in the building code that prevents you from building a stair greater than 12 feet without a landing. In the IRC 2018, this particular restriction has been adjusted to approx 12'-6". As always, check your local code to determine your requirements.
Note: A structural engineer is needed for any floor-to-floor heights greater than 11'-7" according to the IRC. Regardless of the code we recommend working with a structural engineer no matter the project.
Truss Coordination
The biggest challenge with trusses is the increased coordination between the design team, suppliers, and construction team. Because the trusses are manufactured in a factory and made to fit, it is not uncommon to have on-site errors in low coordination efforts. For complex projects, having the design team (architect and engineer) review the shop drawings prior to manufacturing is highly recommended. In my experience, I have yet to receive a perfect set of shop drawings that did not need some level of adjustment after our team's review of the truss shop drawings. Most of the time there are just too many moving parts related to structure, HVAC, etc. Having your design team involved in the process can save thousands in on-site repair.
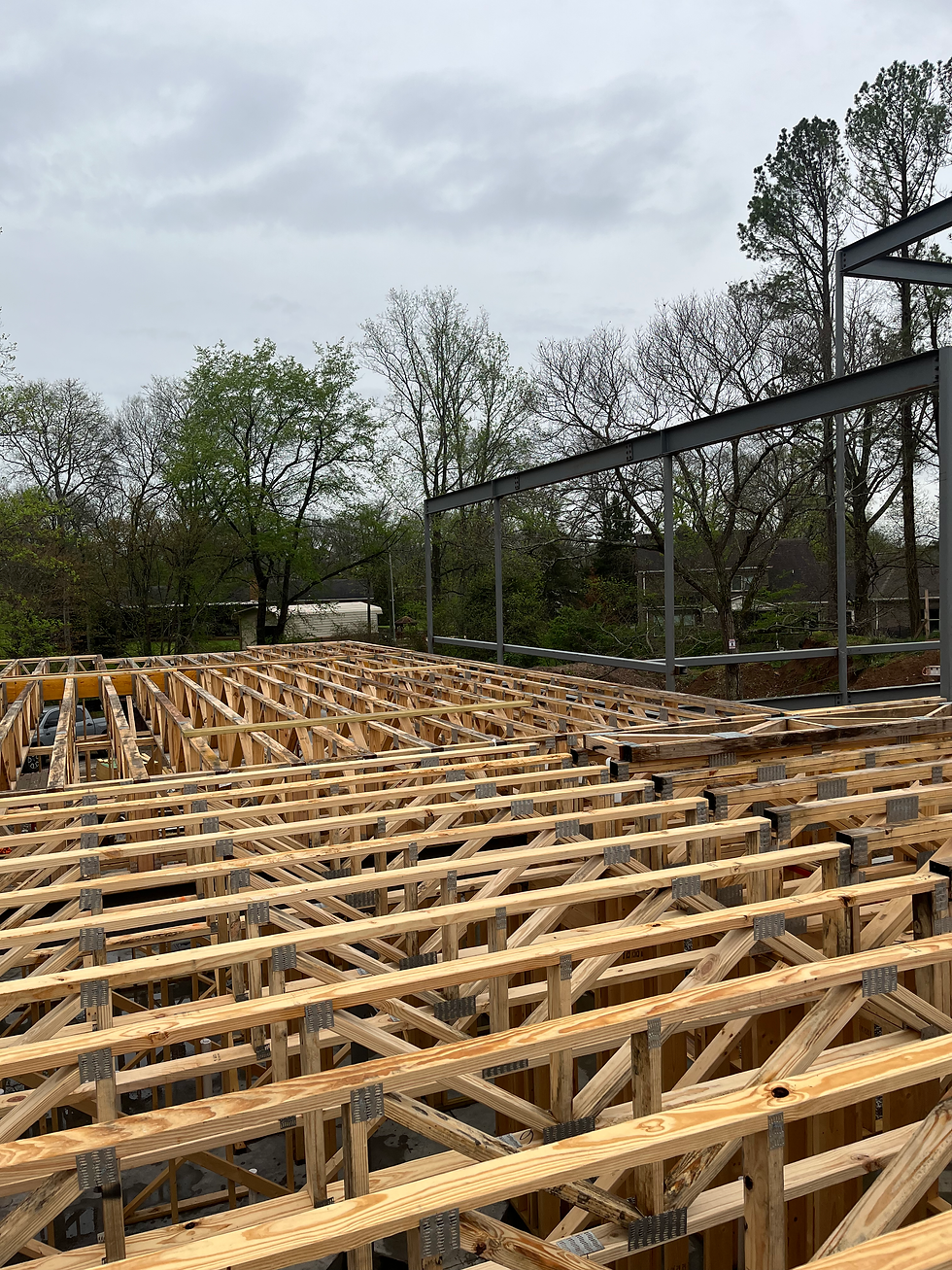
Truss Repairs
When coordination efforts fail the next step is what we call "truss repairs." Truss repairs are simply the on-site modifications of the trusses. Trusses are individually engineered to receive specific loads depending on their location in the project. Any change to the truss must go through the engineering process to confirm the modified truss can carry the specific loads. If a truss repair is needed the contractor communicates the issue with the truss company and an additional shop drawing is prepared to provide the contractor with specific instructions on how to make the modification. This can create time delays and should be avoided if possible. Once again, it is important to have the design team help review the repairs to help identify any additional issues related to the repair. The repairs could impact other structural elements, plans for ductwork, or lighting plans.
Pro Tip: Communication is key to any project. It is not uncommon for truss companies to misinterpret the intent of the truss repairs simply because they are not out on-site. Make sure that photos are being shared with the truss company to help communicate the issues.
To summarize floor trusses offer a lot of benefits and in my opinion, are one of the best products to use in wood construction. We typically spec them on our projects unless we begin running into floor-to-floor height-related issues. As always, subscribe to our blog to stay updated on the latest information.
© 2023 by Clements Wimsatt Architects PLLC
Comments